Running hours and starts
The Running hours and starts section presents usage data about the hoisting motor from the selected timeframe.
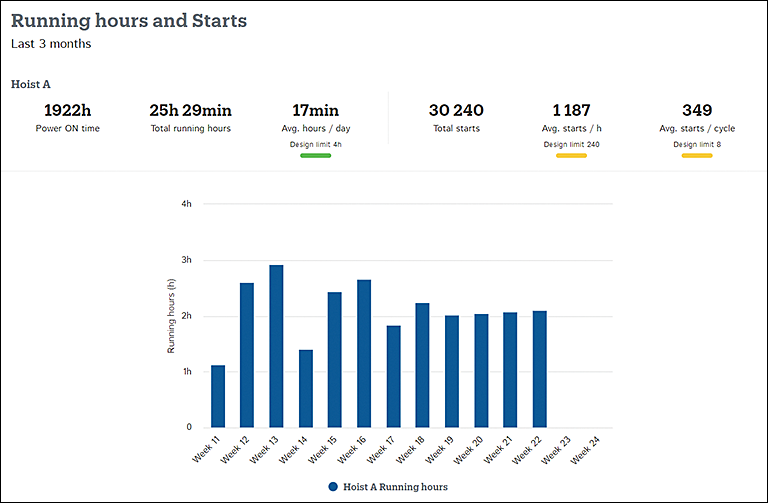
Above the graph, a set of values related to running hours and starts are presented. There are both actual recorded values and calculated average values. The average values are compared to their respective design limits, which are presented below the averages. The following table reflects the design limits for daily running hours and hourly starts, with respect to the design class of the hoist.
Class | ISO/AS | FEM | CMAA | Running hours / day | Starts/h |
---|---|---|---|---|---|
3 | M3 | 1Bm | A | 1 | 150 |
4 | M4 | 1Am | B | 2 | 180 |
5 | M5 | 2m | C | 4 | 240 |
6 | M6 | 3m | D | 8 | 300 |
7 | M7 | 4m | E | 16 | 360 |
8 | M8 | 5m | F | 16+ | 360 |
Design limits should not be exceeded in normal operation. If the design limit has not been exceeded during the last three months, the indicator color below the value is green. If the design limit has been exceeded, the color turns yellow. Yellow color indicates the hoist being over-worked compared to its design, causing its service life to shorten faster.
Here are detailed explanations for each of the actual and average values that are visible above the graph.
- Power ON time: Total actual time during which the DMU has been powered on over the selected timeframe. Presented in hours or minutes. If the power-on time is significantly higher than the total running hours, it means that the crane is idling most of the time: so, powered on without any ongoing hoisting operations. A crane consumes electricity while idling. You can cut down electricity consumption by powering off the crane with the emergency stop button whenever it is not needed for production.
- Total running hours: Actual total running time of the hoisting motor from the selected timeframe. Both running time with a load and without a load are considered. Presented in hours or minutes.
- Avg. hours / day: Daily average number of running hours or minutes. If the Avg. hours / day exceeds the design limit, pay attention to the inspection of the rotating components, such as the motor, coupling, gear reducer, and drum bearings.
- Total starts: Total number of hoisting motor starts from the selected timeframe. A start refers to a hoisting motor start, with the movement being up or down.
- Avg. starts / h: Average number of hoisting motor starts in an hour. If the Avg. starts / h exceeds the design limit, pay attention to the inspection of the hoisting motor.
- Avg. starts / cycle: Average number of hoisting motor starts in a hoisting cycle. One hoisting cycle should normally be no more than eight starts. If that ratio is exceeded repeatedly, the hoist is used in a jogging manner, meaning that the load is lifted or lowered in small increments. So, the hoisting motor gets exposed to repeated starts and stops. Jogging reduces the lifetime of the hoist, adversely affecting both its mechanics and electrics—the brake and contactors in particular.
The bar graph presents the running time trend over the selected timeframe, allowing you to spot any excessive peaks in usage. Common causes of excessive running hours include the following.
- Operator behavior
- Process flow
- Long lifts
- Excessive use of the slow-speed motion
- Long running periods at peak production demands
You should then be concerned about the following.
- Productivity
- Condition and temperature of the hoisting motor
- Reduced service life of the hoist
- Wear of other crane components, such as the bridge, trolley, and drive
The recommended actions are as follows.
- Arrange operator training
- Conduct an application study to determine whether the crane or hoist suits the current production and operating demands
- Investigate other Demag control technology
- Review the inspection and preventive maintenance schedule to ensure compliance with the instructions of the manufacturer