Events and alerts
This subsection lists all alert and event messages from the selected time frame.
The messages have been grouped. First, the number of different types of alert and event messages is shown for the crane level. Next, we have a separate section for each hoist and crab.
The traffic light logic of this subsection is as follows: If even one value is red, the overall status is red. If there are no red statuses, the overall status is green. There is no yellow status.
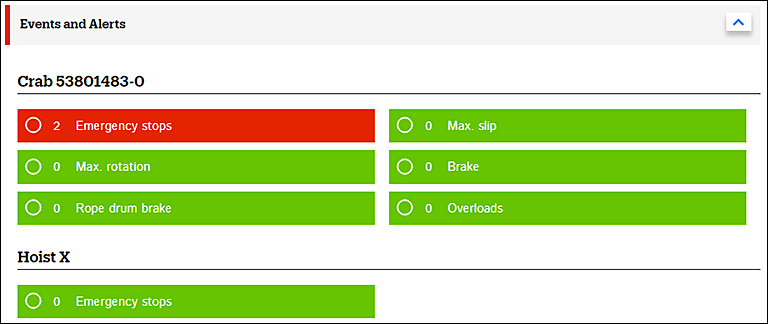
Emergency stops
This value reflects the cumulative number of emergency stops from the selected time frame.
An emergency stop is registered when the operator stops the motions of a machinery abruptly during a lifting, lowering, traveling, or traversing movement. The operator can either press the emergency stop button of the radio controller or turn the key switch of the pendant controller. So, the emergency stops count contains only such emergency stops that occurred while a machinery was in motion.
Emergency stop occurrences raise concern about the following:
- True emergency
- Operational safety
- Use of the emergency stop button on the pendant controller as a regular control device
- Shock loading
The recommended action is to find out the causes of the emergency stops and arrange operator training if necessary.
NOTE | As the reasons for emergency stop occurrences may be indicative of a safety issue, each occurrence should be investigated. |
Overloads
This value reflects the cumulative number of attempted overloads from the selected time frame.
An overload occurs when the lifted load exceeds the rated capacity of the hoist. Hoists are equipped with overload protection devices, which are designed to prevent lifting beyond a set limit. StatusControl records the cumulative number of overload occurrences.
The following can cause repeated overload occurrences:
- Operator error
- Attempting to lift loads beyond the rated capacity
- Shock loading or starting to lift a load in high speed
- Improper rigging
- Improperly calibrated load monitoring device
- Improper use of non-fixed load-lifting attachments
You should then be concerned about cumulative fatigue or damage to various components, such as hooks, sheaves, wire ropes, rope drums, gear reducers, couplings, motors, and brakes. The recommended action is to arrange operator training to address rigging, crane controls, load swing, and preoperational inspections.
Braking distance
This value reflects the effectiveness of the brake. The calculation is based on the encoder pulse count.
If the value that has been entered in parameter “Wear limit / coasting (brake)” is exceeded during a braking process, it indicates a faulty behavior. The reason can be, for example, brake wear or a change in the friction coefficient due to oily surfaces.
Maximum slippage
This value is the number of errors 22 and 38 (slip error) that occurred in the lifting axis.
The value is used for analysis and error evaluation of installation problems.
Maximum rotation
This value is the number of errors 18 and 19 (speed errors) that occurred in the lifting axis. For example, the value was exceeded or the value was below the specified speed and incorrect direction of revolution was detected.
The value is used for analysis and error evaluation of installation problems.
Brake
This value reflects the number of times when the maximum braking path was exceeded or an error signal from the monitoring contact of the hoisting brake was received.
The value is used for analysis and error evaluation of installation problems.
Rope drum brake
This value shows the number of catching operations that were carried out by the optional rope drum brake.
The value is used for analysis and error evaluation of installation problems.